Mester filter bags are used in steel blast furnace dust removal, with high temperature resistance to intercept metal dust
Jul 17,2025
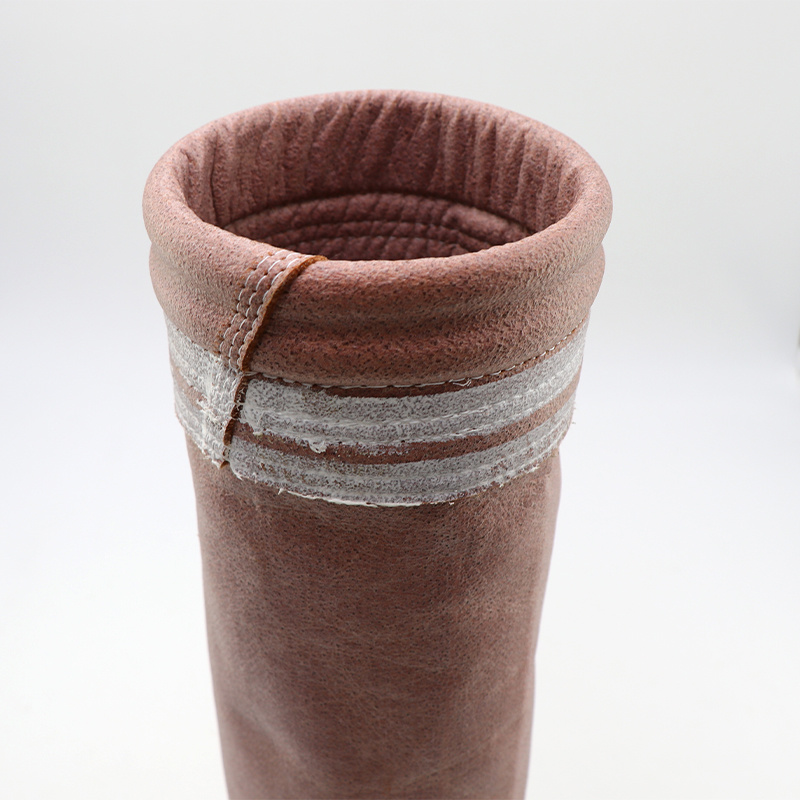
Core Characteristics of Meister Filter Bags
1. Excellent High-Temperature Resistance
Operating Temperature: Can continuously operate at 180–204℃, with instantaneous temperature resistance up to 220–260℃, and a thermal shrinkage rate of less than 1% (at 250℃).
Thermal Stability: Stable molecular structure at high temperatures, no risk of coating shedding, avoiding secondary pollution.
Flame Retardancy: Starts to carbonize at 400℃, limiting oxygen index (LOI) reaches 30, non-self-igniting, and non-combustible.
2. Chemical Corrosion Resistance
Tolerates acidic and alkaline environments with pH values of 2–12, and has good resistance to low-concentration acids, alkalis, sulfides (such as SO₂, H₂S), hydrocarbons, and a small amount of fluorides.
The lifespan in sulfur-containing flue gas can reach more than 3 times that of ordinary filter bags.
3. Excellent Physical and Mechanical Properties
High Strength: Radial tensile strength >800N/5×20cm, weft direction >1200N/5×20cm, seam strength retention rate 95%.
Abrasion and Bending Resistance: Smooth and dense surface, abrasion resistance is 4–6 times that of fiberglass, and bending resistance is improved by 3 times.
Air Permeability and Precision: High air permeability, operating resistance 800–1200Pa, can capture particles around 0.3μm.
Application Fields of Meister Filter Bags
1. High-Temperature Heavy Industry Fields
Iron and Steel Metallurgy: Used for intercepting high-temperature dust in blast furnace gas, converter flue gas, sintering machines, etc., resisting corrosion from iron oxides and sulfur-containing gases.
Cement Production: Processing kiln tail gas (180–250℃), preventing the caking of high-alkaline dust, and ensuring system air permeability.
Incineration of Waste: Purifying high-temperature flue gas from incinerators, efficiently filtering acidic gases (such as HCl, SO₂) and toxic substances such as dioxins.
2. Energy and Chemical Industry Fields
Coal-fired/Biomass Power Plants: Adaptable to boiler flue gas temperature fluctuations, resisting coal ash wear and biomass wet heat corrosion.
Coke Industry: Purifying sulfur-containing coke oven gas, benzene, and ammonia, preventing chemical corrosion leading to filter bag embrittlement.
Chemical Production: Processing reactor tail gas, viscous particles and organic solvent volatiles in carbon black production processes.
3. Special Working Condition Fields
Asphalt Mixing Station: Resisting tar-like sticky dust, reducing the risk of bag clogging, and extending the cleaning cycle.
Non-ferrous Metal Smelting: Intercepting metal oxides in electric furnace dust, withstanding high-temperature oxidation environments.
Industrial Boiler Flue Gas: Compatible with complex flue gas components from the combustion of various fuels such as gas and oil.
4. High-Precision Filtration Scenarios
Ultrafine Dust Capture: Using PTFE membrane technology for submicron particle filtration in industries such as pharmaceuticals and lithium battery materials.
Explosion-proof Environment: Adding anti-static fibers, suitable for explosive dust conditions such as coal powder preparation and aluminum/magnesium processing.
PREVIOUS:
Related Posts
Contact Us
E-mail:
gdkaidun@163.com
Phone/WeChat:
86-131-3828-6677
Address:
Room 401, Building 21, No. 1, Keqing Road, Yundonghai Street, Sanshui District, Foshan City, Guangdong Province