Polyimide hydroentangled nonwovens are used in high-temperature applications such as high-temperature gas/liquid filtration and welding clothing.
Jul 17,2025
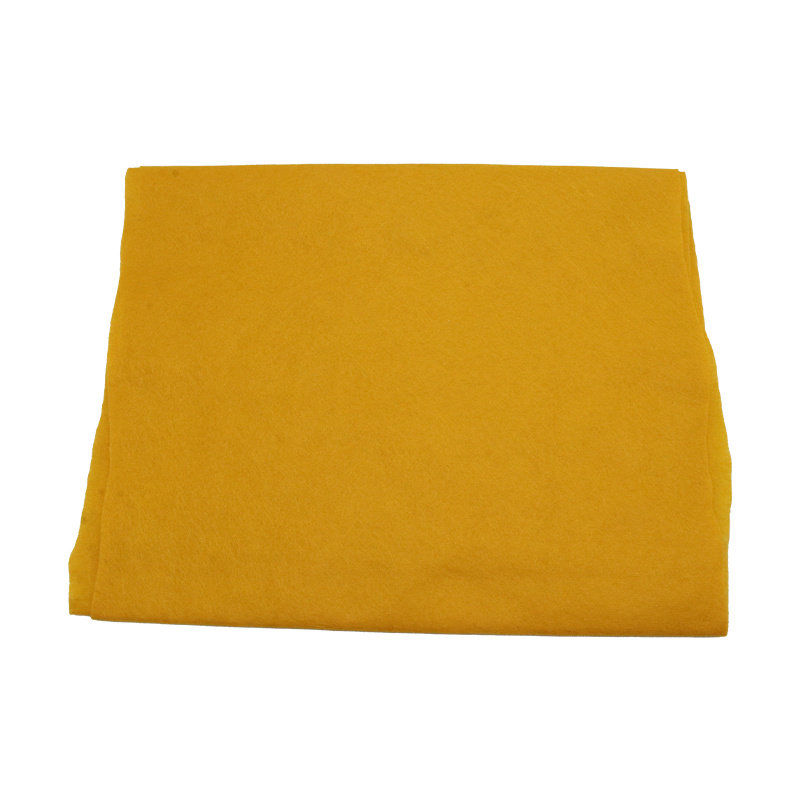
Polyimide (PI) hydroentangled nonwovens are high-performance materials that combine the excellent inherent properties of polyimide with the unique structure of hydroentanglement nonwoven technology.
Basic Properties of Polyimide Hydroentangled Nonwovens
High-Temperature Resistance:
The long-term use temperature is typically above 260°C, and the short-term exposure temperature can exceed 400°C (even up to 500°C).
It maintains excellent physical and mechanical properties and dimensional stability at high temperatures, and is not easily melted, shrunk, or embrittled.
The fiber entanglement structure formed by hydroentanglement technology also maintains good integrity at high temperatures.
Chemical Stability:
It has excellent resistance to most organic solvents (such as alcohols, ketones, hydrocarbons, esters, etc.).
It exhibits excellent resistance to strong acids (except concentrated sulfuric acid and concentrated nitric acid) and strong alkalis (except concentrated sodium hydroxide).
It has good hydrolysis resistance and can be used stably for a long time in humid or steam environments.
Thermal Stability and Flame Retardancy:
It has a high limiting oxygen index (typically >38), is an inherently flame-retardant material, self-extinguishes when away from an open flame, and does not produce melt droplets.
Thermal decomposition is slow at high temperatures, with low smoke generation and minimal release of toxic gases, meeting stringent fire safety standards.
Good Mechanical Properties:
High strength, high modulus, and good wear resistance.
Hydroentanglement technology gives it good flexibility, drape, and delamination resistance (compared to traditional woven or knitted PI fabrics).
It has good tear strength and burst strength.
Low Dielectric Constant and Low Dielectric Loss:
Excellent electrical insulation properties, remaining stable even in high-temperature and high-frequency environments.
The dielectric constant is typically around 3.0-3.5, and the dielectric loss tangent is low.
Low Coefficient of Thermal Expansion:
Minimal dimensional change with temperature, high thermal stability.
Radiation Resistance:
It has good resistance to γ-rays, X-rays, electron beams, and other radiation, with slow performance degradation.
Good Filtration Performance:
Hydroentanglement technology can form a complex, uniform three-dimensional microporous network structure with high porosity and controllable distribution.
Fiber fineness is adjustable, enabling filtration accuracy from coarse to high efficiency.
The surface is smooth, does not easily adhere to dust, and has a certain self-cleaning ability (compared to needle-punched technology).
Low Moisture Absorption:
Low moisture absorption rate, stable performance in humid environments, and electrical insulation is not easily reduced.
Application Fields of Polyimide Hydroentangled Nonwovens
High-Temperature Gas/Liquid Filtration:
Industrial High-Temperature Dust Filtration: Core filter material for dust collection bags in high-temperature flue gas from garbage incinerators, coal/gas-fired boilers, cement kilns, metallurgical furnaces, chemical reaction furnaces, etc. It can withstand the mechanical force of pulse cleaning and has a long service life.
High-Temperature Air Filtration: Clean rooms, semiconductor manufacturing, spray painting workshops, and other occasions requiring high-temperature air treatment.
Hot Oil/Hot Gas Filtration: High-temperature media filtration in chemical, petrochemical, and lubricating oil production processes.
Electrical Insulation and Electronics:
High-Temperature Insulation Materials: H-class (180°C) and above motors, generators, transformers, slot insulation, interphase insulation, and pad insulation for electromagnetic wires, etc.
Flexible Circuit Substrate/Reinforcement Material: Used in FPCs requiring high heat resistance and high reliability.
Battery Separator: Especially suitable for lithium-ion batteries (especially power batteries and energy storage batteries) with extremely high requirements for high-temperature safety and dimensional stability, preventing thermal runaway. Good resistance to electrolyte corrosion.
Electromagnetic Shielding Material Substrate: Used to manufacture electromagnetic shielding materials in high-temperature environments.
Protective Clothing and Thermal Insulation Materials:
Firefighting suits, welding suits, and protective clothing for furnace workers: As a heat insulation layer or outer layer, it provides good high-temperature and flame protection and a certain degree of chemical protection.
Aerospace: Heat insulation and fire protection layer for aircraft engine compartments, and heat insulation layer for spacesuits.
High-Temperature Industry: Heat insulation and fire protection wrapping materials for high-temperature pipelines and equipment.
Friction Sealing Materials:
Used as a reinforcing substrate for high-performance brake pads, clutch plates, and sealing gaskets, providing dimensional stability and strength at high temperatures.
Composite Material Substrate:
Used as a prepreg or resin transfer molding (RTM) reinforcement material to manufacture high-temperature, high-strength composite parts (such as aerospace structural parts and racing car parts). 。
Special Packaging and Sealing:
Packaging for special items requiring high-temperature sterilization (such as steam sterilization) or long-term high-temperature storage.
Sealing gaskets for high-temperature environments.
Related Posts
Contact Us
E-mail:
gdkaidun@163.com
Phone/WeChat:
86-131-3828-6677
Address:
Room 401, Building 21, No. 1, Keqing Road, Yundonghai Street, Sanshui District, Foshan City, Guangdong Province