Aramid fabric application in construction engineering
Jul 21,2025
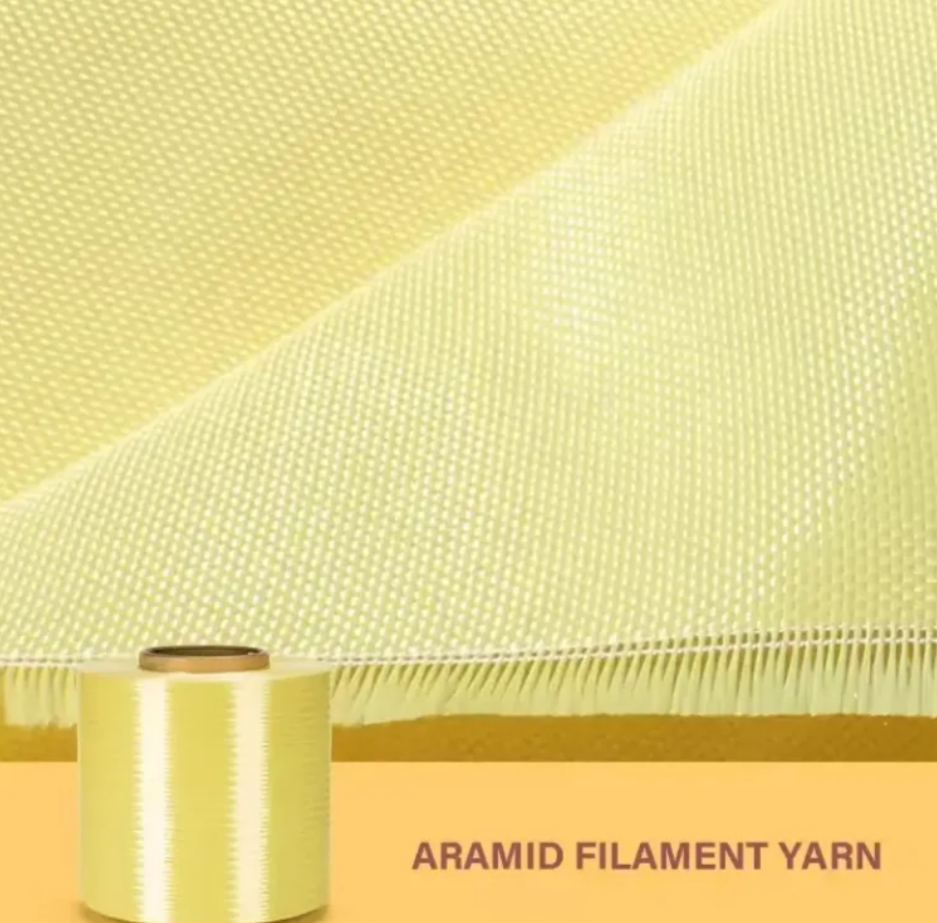
Aramid fiber is a new type of high-tech synthetic reinforcing fiber material. It is bonded to concrete components through epoxy adhesive, and they work together to enhance the load-bearing capacity of the components. It is mainly used in the reinforcement and repair of structures in subway tunnels, stations, electric railway tunnels, computer rooms and other buildings requiring insulation, and infrastructure such as transportation, water conservancy, nuclear power, and energy. The discovery of aramid is considered a very important historical process in the materials field.
According to research reports released by the laboratory, aramid has a variety of excellent characteristics. ① Impact resistance :It has good ductility. Aramid material first absorbs a large amount of energy through deformation, and its failure mode is ductile failure. In contrast, the failure mode of carbon fiber is brittle failure. ② Dynamic load and fatigue resistance :Carbon fiber has high tensile strength, but the failure mode of carbon fiber is brittle failure, which can only withstand long-term static loads. Aramid fiber has unique advantages in fields with high requirements for dynamic load and fatigue resistance. Therefore, when carrying out structural reinforcement, attention should be paid to the characteristics of stress distribution in the structural reinforcement part, and consideration should be given to using aramid fiber or carbon fiber for reinforcement. ③ Corrosion resistance :Aramid composites have good acid and alkali corrosion resistance. Chloride ions in seawater have strong corrosiveness to concrete structures, which can lead to concrete carbonation and steel bar corrosion. Therefore, aramid fiber composites are more commonly used in the structural reinforcement and protection projects of some seaport wharves. ④ Electrical insulation :Non-magnetic aramid fiber is a non-conductive material. Therefore, in projects such as subways, high-speed railways, instrument rooms, hospitals, and some special industrial plants where insulation requirements are very high, aramid fiber composites are more suitable for reinforcement projects in these fields.
Aramid fiber has good spinnability, can be spun, woven, and can also be stitched by needle punching and hydroentangling, and used to make various protective products. For example, high-temperature-resistant aramid gloves, furnace front work clothes, etc. Aramid products have great application value in heat insulation, flame retardancy, and fire prevention, and can be used in industrial production, construction, automobiles, rail transit, aerospace, new energy, and other fields. In addition, aramid can also be used in building reinforcement.
The application of aramid in construction includes, but is not limited to: shear, bending, ductility, and seismic reinforcement of concrete beams, slabs, and columns; subway tunnels, stations, electric railway tunnels, computer rooms, and other buildings requiring insulation; structural reinforcement and repair of infrastructure such as transportation, water conservancy, nuclear power, and energy.
Aramid fiber, as a reinforcing material, has a coefficient of linear expansion similar to that of ordinary concrete, which ensures that there will be no bonding damage due to temperature changes. After proper treatment (grinding, cleaning, brushing primer) of the concrete surface, and then pasting the aramid fiber, good bonding force between the two can be ensured.
The construction process and flow of aramid used in building reinforcement. First, ① clear obstacles, clean according to the actual situation on site, the general principle is to facilitate construction. ② Lay out and check the lines on the construction site, and lay out the lines and points of the carbon aramid cloth pasting position. After the on-site technician (foreman) verifies that the layout is correct, the construction can begin. ③ Clean the concrete structure surface to be pasted, and grind the concrete surface with an angle grinder. Use a blower to blow away the floating dust on the concrete surface. Then, ④ prepare and apply the primer. Accurately weigh the main agent and curing agent of the matching resin according to the prescribed ratio, put them into a container, and stir them evenly with a stirrer. The amount of mixing should not be too much, and it should be used up within the usable time. “Kaitun” independently produces and develops reinforcing materials. Those in need can contact us directly. Quality assurance and affordable prices. ⑤ Level the concrete structure surface. Fill the concave parts of the component surface with epoxy putty and repair it to a smooth surface. When using epoxy putty in residual repair, the construction should be carried out at a temperature above -5℃ and a relative humidity of less than 85%. After the putty is applied, if there are still uneven textures on the surface, it should be polished smooth with sandpaper, and the corners should be repaired into a circular arc with a radius of no less than 30mm. ⑥ Paste the aramid cloth. Before pasting the aramid cloth, it should be confirmed that the pasting surface is dry. When the temperature is above -10℃ and the relative humidity RH>85%, construction should not be carried out without effective measures. To prevent the aramid fiber from being damaged, a steel ruler and a wallpaper knife should be used to cut the carbon fiber material according to the specified size before pasting. To prevent damage to the material during storage, the amount of material cutting should be cut according to the daily usage. Prepare the impregnation resin and apply it evenly to the component to be pasted, with a thickness of 1-3 mm, thick in the middle and thin at the edges. Roll repeatedly along the fiber direction to squeeze out air bubbles and ensure that the impregnation resin completely penetrates the aramid cloth. Apply the impregnation resin evenly to the surface of the aramid cloth. ⑦ Surface protection. If the reinforced component needs fire protection, a fire-resistant coating can be applied after the resin is cured. Coating should be carried out after the initial curing of the resin, and the relevant standards and construction regulations of the coating used should be followed. Finally, ⑧ acceptance. After completion, the project should be submitted to the supervisor or general contractor for acceptance. Then fill in the hidden inspection information, the acceptance form for the quality of sub-items/sub-projects, and ask the general contractor and supervisor to sign. Organize all the necessary documents for the project and hand them over to the general contractor to ensure the integrity of the entire project documents.
In the evaluation standard of construction quality, the main control item is that the pasting of aramid cloth must meet the design requirements and construction specifications of the reinforcement industry. The general item is that for hollowing with a diameter of more than 10mm and less than 30mm, less than 10 per square meter can be considered qualified. If there are more than 10 per square meter, it is considered unqualified and needs to be repaired. For hollowing with a diameter of more than 30mm, as long as it appears, it is considered unqualified and needs to be repaired.
When aramid fiber cloth is used in the construction of building reinforcement, the following safety matters should be noted: ① The A and B components of the matching resin should be stored in a sealed container, away from fire sources, and avoid direct sunlight. ② Operators should wear work clothes and protective masks. ③ The construction site should be equipped with various necessary fire extinguishers for rescue.
The difference between carbon fiber cloth and aramid fiber cloth
Carbon fiber fabric and aramid fiber fabric are both high-quality fiber composite materials used in reinforcement, but they differ in strength. Carbon fiber fabric, while possessing high strength, is also electrically conductive. Aramid fiber fabric, on the other hand, is not electrically conductive and is suitable for use in electrically charged environments.
In addition, aramid fiber fabric has higher toughness and impact resistance compared to carbon fiber fabric, making it more suitable for use in dynamic load environments. Therefore, when using fiber composite materials for structural reinforcement, the specific material type should be selected based on the actual situation.
Related Posts
Contact Us
E-mail:
gdkaidun@163.com
Phone/WeChat:
86-131-3828-6677
Address:
Room 401, Building 21, No. 1, Keqing Road, Yundonghai Street, Sanshui District, Foshan City, Guangdong Province